The Best Cost-Effective Solution: Maintenance
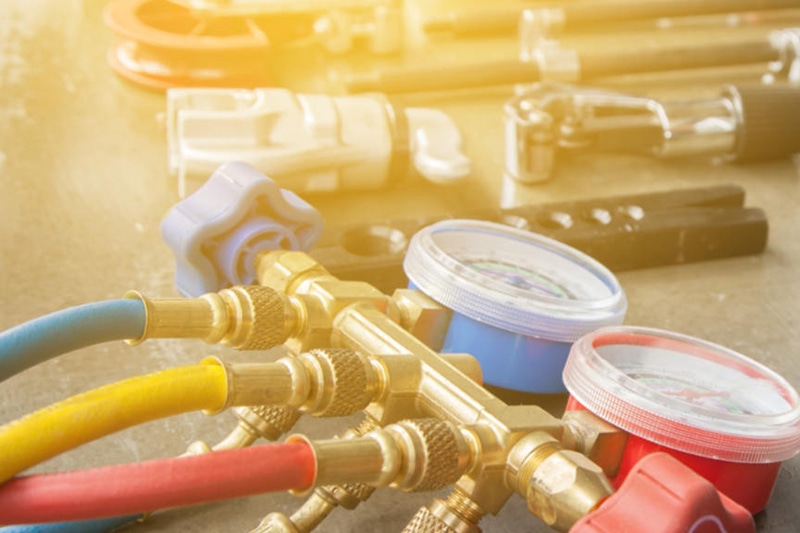
Property managers know that their commercial HVAC system should perform scheduled maintenance service performed but let’s look at why these services are so important and what we do for the HVAC systems that ensures efficiency and longevity.
Scheduled maintenance is necessary and important for the upkeep of your HVAC investment. We ensure the unit is in good working condition and prepare and correct any issues to keep it running efficiently throughout each season to avoid unexpected failures or breakdowns.
Not only will maintenance safeguard your units but can also save you money. Inspections keep your HVAC running at peak efficiency that will save you up to 30% of your energy bill, according to the U.S Department of Energy. And most importantly the real money saver – your unit’s longevity. A well-maintained commercial HVAC should have a lifespan of up to 15-20 years. If not maintained or inspected, the lifespan can be cut almost in half!
So, what exactly do we do in an annual inspection? See below RPM’s detailed checklist that can be individualized for each property and can include much more or less:
Air Cooled Condensing Units
• Remove each chiller from service and lock/tag out electrical service.
• Remove all required panels to access condenser coils.
• Power wash and clean condenser coils.
• Re-install panels and verify chillers have been returned to service.
• Check compressor oil for high acid content.
• Perform refrigerant leak check on each chiller.
• Inspect and tighten all electrical connections.
• Check electrical integrity on compressors and components.
• Check control system operation and perform the follow tasks.
• Tighten and clean all electrical connections.
• Check overloads contractors & starters for proper operation and clean as required
• Inspect all safety and temperature controls and includes high & low-pressure switches, crankcase heaters, freeze stats and oil temperature thermostats, calibrate as required.
• Run machine at full load and log operation.
• Check oil level in each compressor and record.
• Log each chiller and record operating conditions.
Supply Fans
• Check all electrical connections in the motor terminal box, service disconnect and starter panel.
• Inspect contacts on the motor starter.
• Remove inlet screen and side panel.
• Clean hub, blades, inlet cone, side panels and outside of each fan.
• Lubricate the motor bearings.
• Check bearing cap for cracks.
• Check blade assembly for cracks (common with fixed pitch retrofits).
• Re-assemble and return fan to operation.
• Check main air pressure, load and unloading of fans.
• Check and record static pressure and current draw at full load conditions.
• Check fan mounting bolts, backdraft dampers, spring isolators and canvas connector.
• Log each fan and record operating conditions.
Exhaust Fans
• Provide and replace drive belt on each fan.
• Inspect fan assemble and check general condition of equipment.
• Inspect general condition and operation of dampers.
• Check belt alignment and tension and adjust as necessary.
• Check sheaves and bearings and lubricate as necessary.
• Check and record motor operating voltages and amps.
• Log each fan and record operating conditions.
Split-System
• Grease fan and motor bearings. (if applicable)
• Clean the condenser & evaporator coils (annually)
• Check filters and record conditions.
• Test unit operation at full load
• Record suction and discharge line temperatures.
• Record delta temperature on evaporator
• Record current draw for compressors
• Record voltages to unit
• Check refrigeration circuit for leaks.
• Inspect and calibrate operating and safety controls. (if applicable)
• Inspect contactor and starters.
• Inspect and tighten all electrical connections
• Inspect heat exchanger or heating elements.
• Inspect the drain pans.
• Check fan-cycling controls and adjust as necessary.
• Log unit and record operating conditions.
Preventative Maintenance is one of the most important actions you can take as a property manager to avoid the bigger costs and tenant issues. Reliable Plant Maintenance not only provides a unique maintenance schedule for your specific property but will draw up a contract and even give you options on payment plans. We like to call this a ‘set it and forget it’ because you don’t have to worry about scheduling or remembering, we do this for you!
Need Service?
Contact the experts at Reliable Plant Maintenance.
Call us at 469-631-0571!